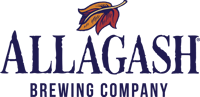
Allagash Brewing Achieved Exceptional Quality While Reducing Product Loss
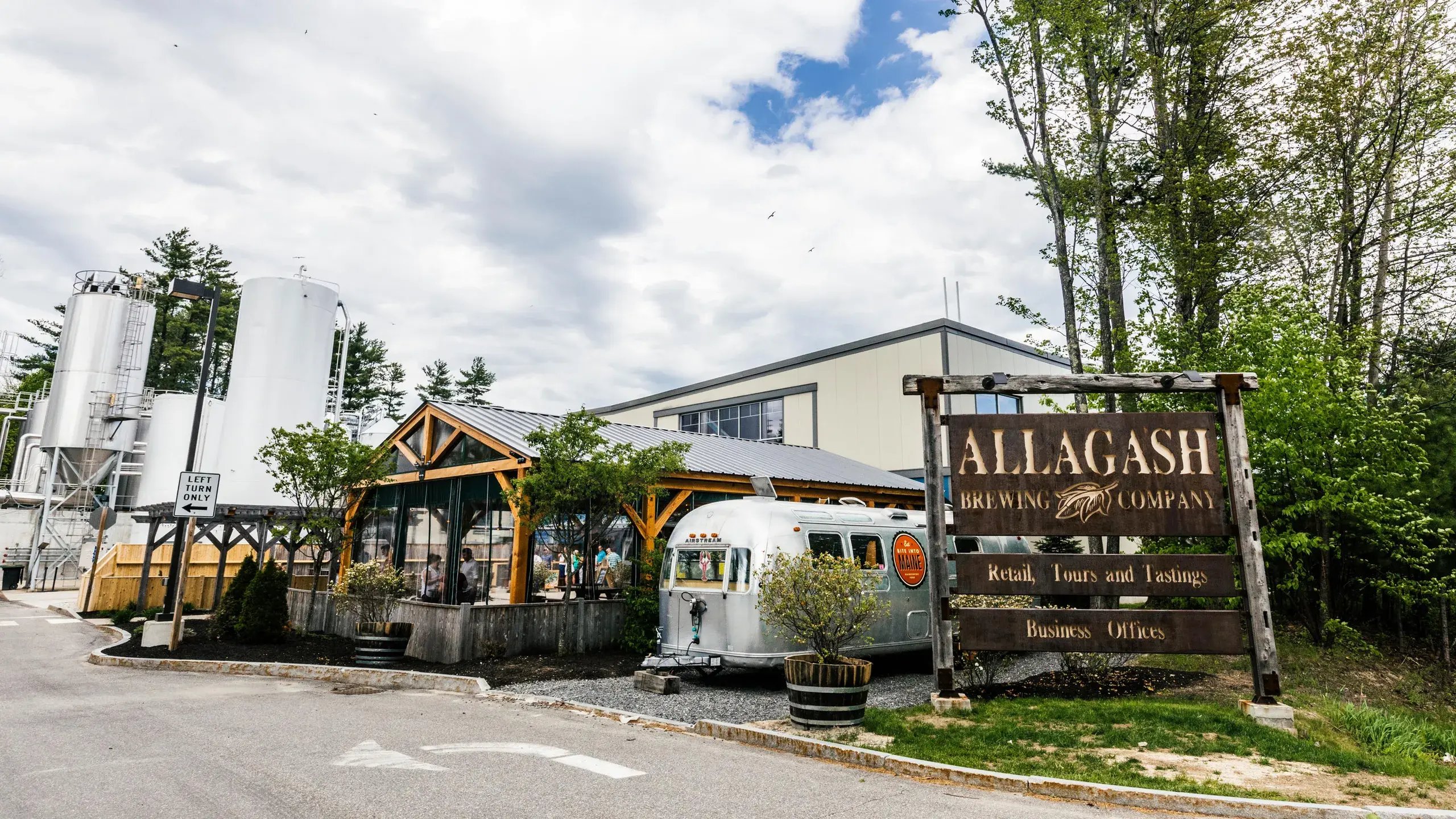
Industry
Brewery
Challenge
Overfilling can be common practice to reduce DO and maintain fill levels, but leads to unnecessary product waste and financial loss. Allagash needed a solution to maintain exceptional product quality while minimizing product loss and achieving precise fill control.
Results
Allagash reduced product loss while maintaining low DO levels. They achieved a 1g variance in can weights, retained more beer per batch, and confirmed superior quality without overfilling.
Products
Can Supply, ACS V5
Our customers are quality focused. Precision filling technology that enables them to package the absolute best quality product, while still keeping product loss below 1% is key to their brand integrity and ensuring they sustain and grow profitability.
Michael Slopek
Head of Customer Success @ Cask
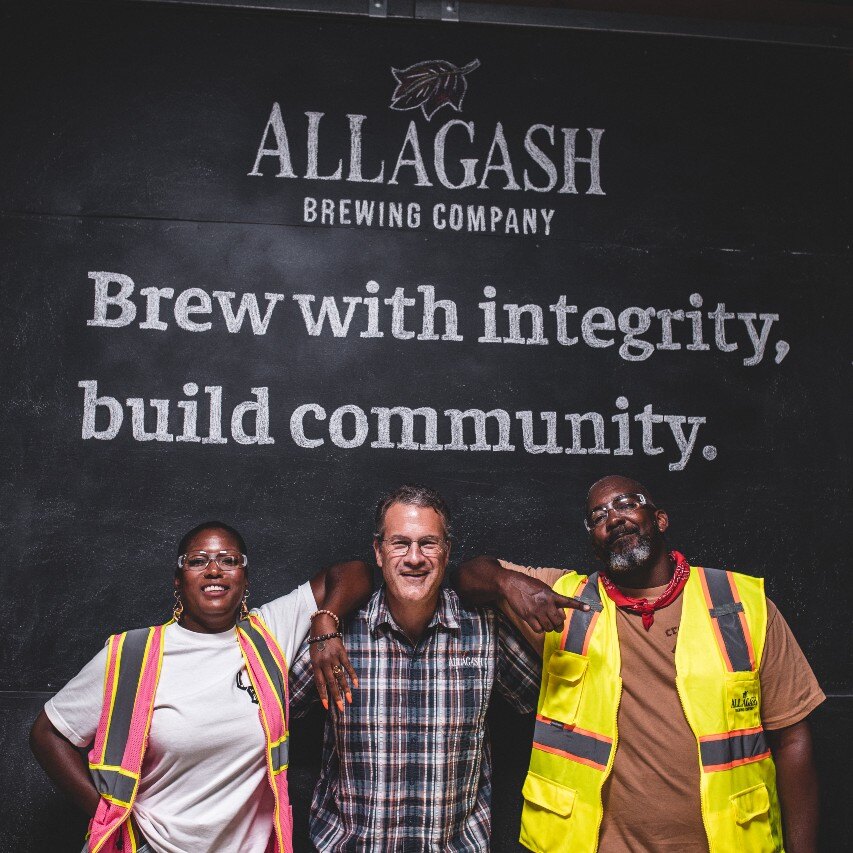
About Allagash Brewing Company
Allagash Brewing Company is a bellwether of craft beverage, renowned for their dedication to quality. When they sought to offer their iconic Allagash White in cans, they trailblazed a new path for traditional-style brewers to explore formats beyond the glass bottle. Now, cans of Allagash White can be found in 23 states across the U.S.
Their commitment to sustainability, community and quality is second to none in the industry.
The Challenge
Product loss is often difficult to quantify, as it can occur in various ways throughout the packaging process. Overfilling cans is a common yet costly practice, used to reach consistent fill levels and low total packaged oxygen (TPO). However, this method leads to unnecessary product waste and is very costly over time. Minimizing liquid dissolved oxygen (DO) and TPO can be achieved by effectively filling the headspace of the can with foam with the right filling technology, reducing oxygen pickup and preserving beer quality.
Allagash Brewing Company, as the leader in craft beer innovation, needed to maintain their high-quality standards while introducing cans to the market. Using one of the earliest ACS V5 canning systems, they sought to tackle key challenges:
-
Achieve low dissolved oxygen (DO) without overfilling.
-
Maintain fill accuracy to control product loss.
-
Ensure consistent package quality and stability across production runs.
The Solution
Through a comprehensive data analysis of over 1,000 samples, Allagash optimized their canning process and minimized unnecessary product loss. The evaluation focused on:
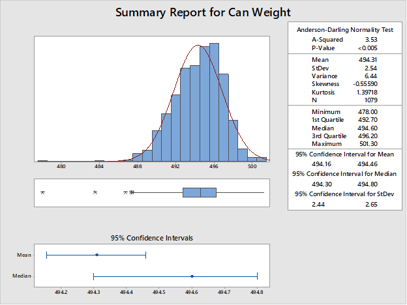
Fill Accuracy Data showed that 95% of can weights fell within a tight 1g variance, validating +/- 3g weight tolerance.
Dissolved Oxygen Control Median DO measurements were 15 ppb, with a 95% confidence interval for a median TPO of 92.4 ppb. This demonstrated that low DO levels could be consistently achieved without product waste.
Process Optimization Optimized purge and underlid CO2 pressures and foam control settings to further refine DO control while maintaining optimal fill precision.
Quality Validation A combination of lab-grade instruments and a trained sensory panel ensured that canned beer met the same high standards as bottled beer before being released to consumers.
The Results
Allagash validated achieving superior packaged quality does not require overfilling. Precise filling technology reduces waste while maintaining the highest product standards.
- Minimal Product Loss: By eliminating the need for overfilling, they retained more beer per batch, leading to substantial cost savings.
- Exceptional Package Quality: Optimized CO2 settings and foam control allowed them to maintain low DO without introducing excess variability.
- Data-Driven Confidence: Over 1,000+ samples confirmed a consistent, repeatable process with minimal can weight and DO variability across different fill heads.
Optimize profitability and sustainability without compromising product integrity. To see how much revenue is on the table for high product loss, check out this interactive chart: Overfilling Effects on Revenue.
Related case studies
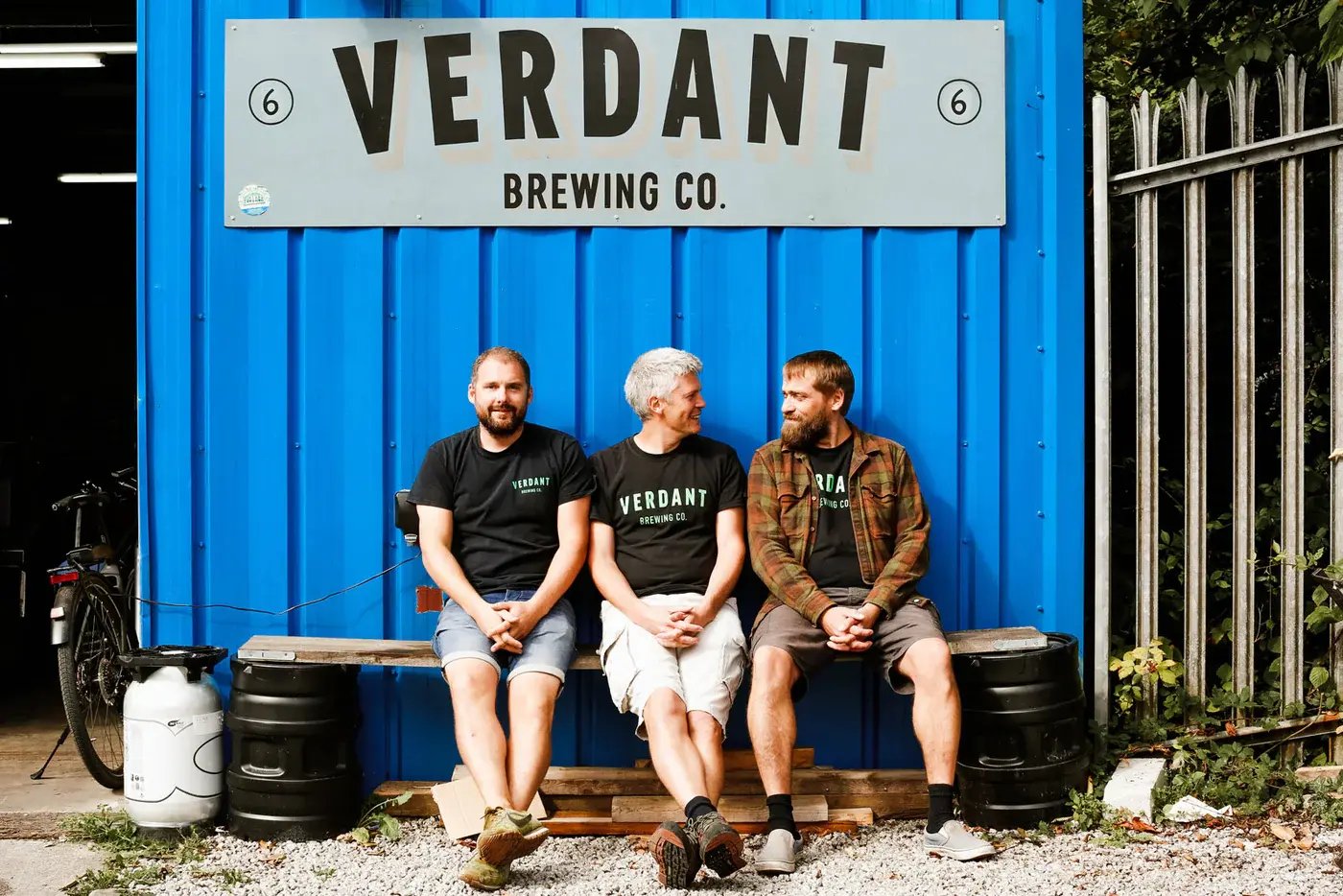
Verdant Brewing Co. Fuels Flexibility and Freshness with Can Supply That Keeps Up
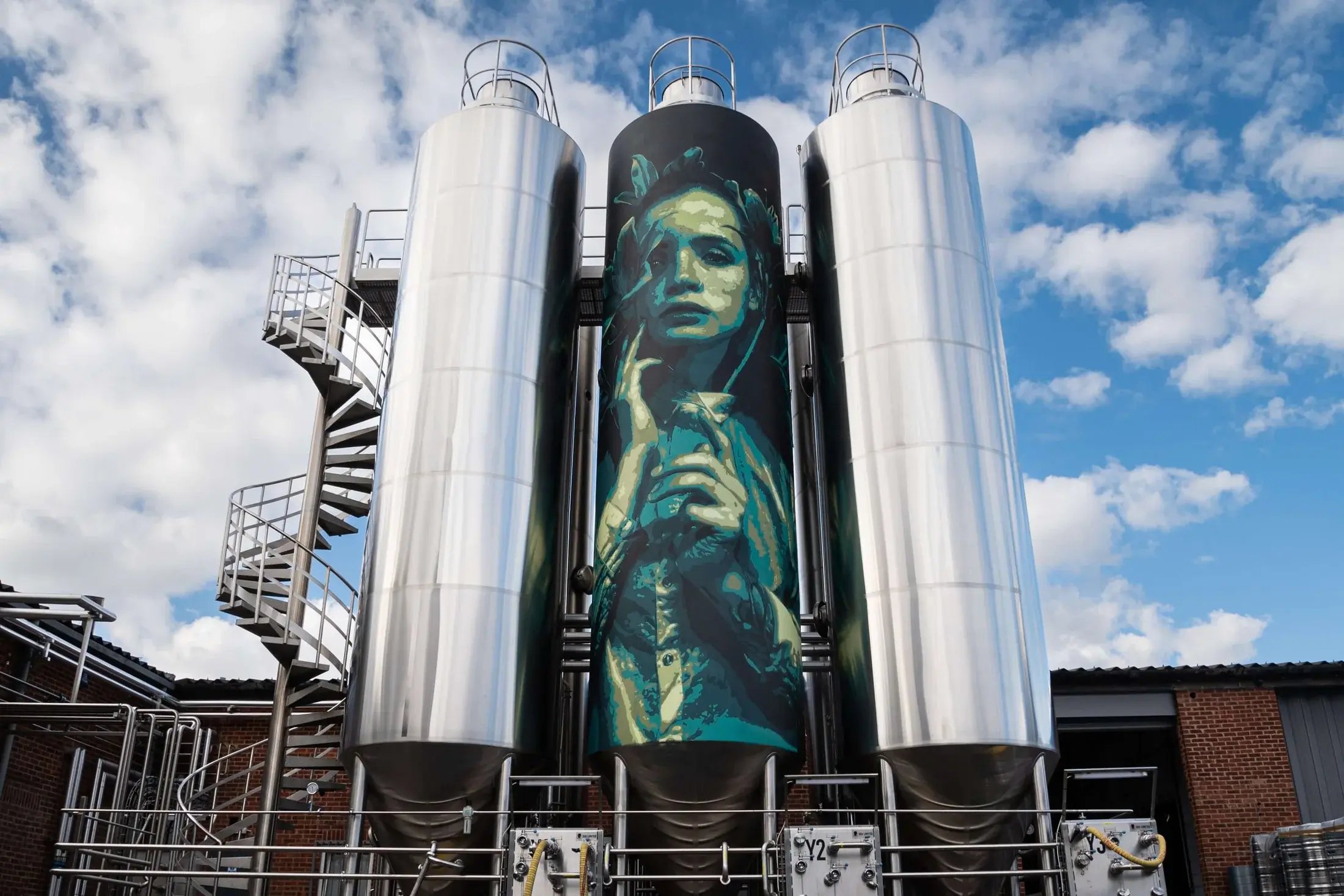
Northern Monk Ditched Direct Supply of 9M Cans Annually In A Bold Move To A Relationship-Driven Distributor
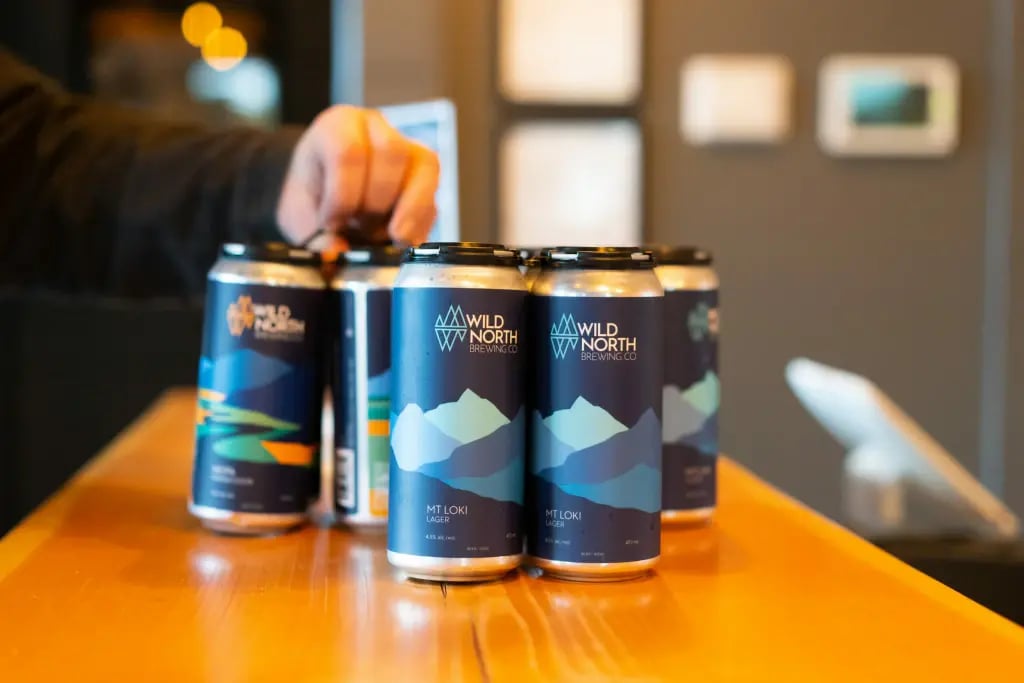