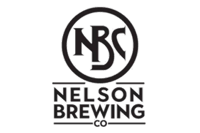
Nelson Brewing Transformed Operations With Automation and Custom Layout Solutions
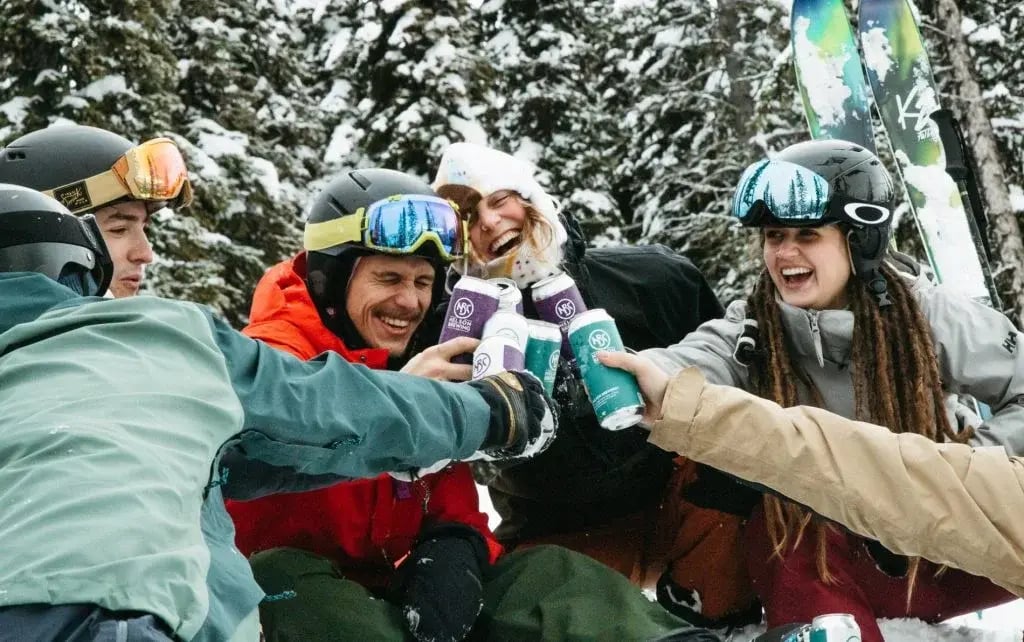
Industry
Brewery
Challenge
For 20 years Nelson Brewing operated their trusted Cask ACS V4 system but needed to modernize to enhance capacity, staff well-being, and automation. With major space constraints they needed a comprehensive, custom solution.
Results
Through a custom layout and advanced automation with the ACS V6 system, Nelson Brewing overcame space constraints to boost production capacity by 40% and create a safer, more ergonomic workplace—improving the efficiency and quality of life for their team.
Key Product
ACS V6, Automated Depalletizer
Designing the right solution isn’t just about technology—it’s about understanding how teams work. With Nelson Brewing, there was a massive opportunity to reimagine their production space, not only increasing their capacity but creating an environment where their staff could thrive. It’s fulfilling to see a custom layout unlock such potential.
Jay Pocza
Automation Specialist & Engineering Technologist @ Cask
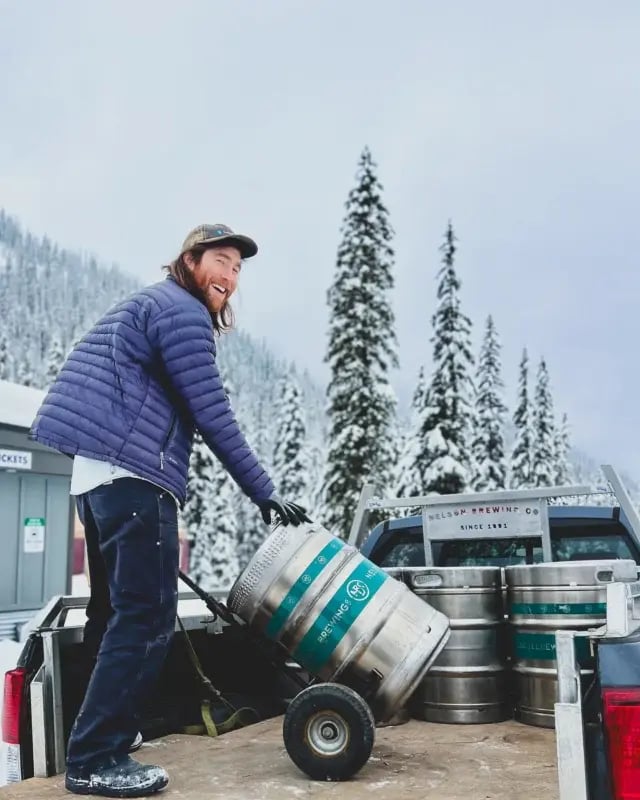
About Nelson Brewing Co.
Nelson Brewing Company has been a pillar of craft brewing since 1991, operating in the historic building that once housed the town’s original brewery. Surrounded by the majestic mountains of British Columbia, their brewery is not just a place to make beer—it’s a community hub. From their subterranean beer cellar featuring a natural creek to their commitment to bringing people together, Nelson Brewing stands as a shining example of craft beer culture.The Challenge
In the craft beverage industry, success relies not only on exceptional products but also on the well-being and satisfaction of the teams behind the scenes. For Nelson Brewing Company, their ACS V4 canning system had been a reliable workhorse for two decades, but as demand grew, so did the strain on their operations team. The manual labor required by their outdated system, coupled with long production hours and suboptimal ergonomics, began taking a toll on their staff.
Reducing physical strain, streamlining repetitive tasks, and enhancing safety weren’t just operational goals—they were essential to creating a better quality of life for their team. By focusing on employee well-being, Nelson Brewing saw an opportunity to foster happiness, boost retention, and free up staff to focus on other areas of the business, multiplying their operational effectiveness. However, integrating modern automation and a Depalletizer into their facility presented a major challenge due to significant space constraints. They needed to reimagine their production space to unlock both efficiency and staff satisfaction.
The Solution
Nelson Brewing collaborated with Cask to deliver a custom-tailored solution that addressed their specific needs with an upgraded ACS V6 & Automated Depalletizer.
Operational Efficiency & Quality of Life
Enhanced Automation of key automation components—including a Depalletizer, Labeller, Rotary Collection Table, Inline Weigh Scale and added conveyance—streamlines processes and enables the entire canning line to require only one full-time designated operator. This is a remarkable improvement from the previously labor-intensive, manual process they experienced.
Ergonomics and Workflow Improvements reduced physical strain for the staff and improves safety, thanks to automation that minimized repetitive tasks and facilitates a cleaner, quieter, and more comfortable workspace.
Space Contraints & Footprint
Custom Layout Design to overcome significant space constraints, Cask customized a switchback layout for the Quick Change Rinse Inverter at the infeed—including a UV-C and Ionized Air Treatment add-on—effectively eliminating the footprint between the Automated Depalletizer and the canning system.
This innovative configuration maximized space usage and allowed for unprecedented production capacity gains within a tight facility.
The Results
Nelson Brewing transformed their production space with their new ACS V6 canning system, implementing a custom-designed switchback layout. This design allows the Depalletizer and other components to fit seamlessly into their constrained space, unlocking production capacity that had previously seemed impossible. The upgraded equipment creates production capacity increase of 40%, enabling the brewery to meet growing demand while maintaining their high standards of quality.
The automation improvements are equally game-changing. By integrating a Depalletizer, Labeller, Rotary Collection Table and Inline Weigh Scale into their line, Nelson Brewing transitions from a manual, labor-intensive operation to a streamlined process that requires one designated full-time operator. This shift not only frees up staff for other critical tasks but also significantly reduces physical strain and repetitive motions, leading to happier, more productive team members.
With waste reduction potential of 50%+, they will achieve substantial cost savings, reinforcing the ROI of their investment in updated equipment. Beyond efficiency and cost, the quieter, cleaner, and more ergonomic workspace foster a positive work environment, improving both team morale and operational consistency.
Nelson Brewing not only addressed their current challenges but also future-proofed their operations, ensuring their packaging process could scale alongside their growth.
Related case studies
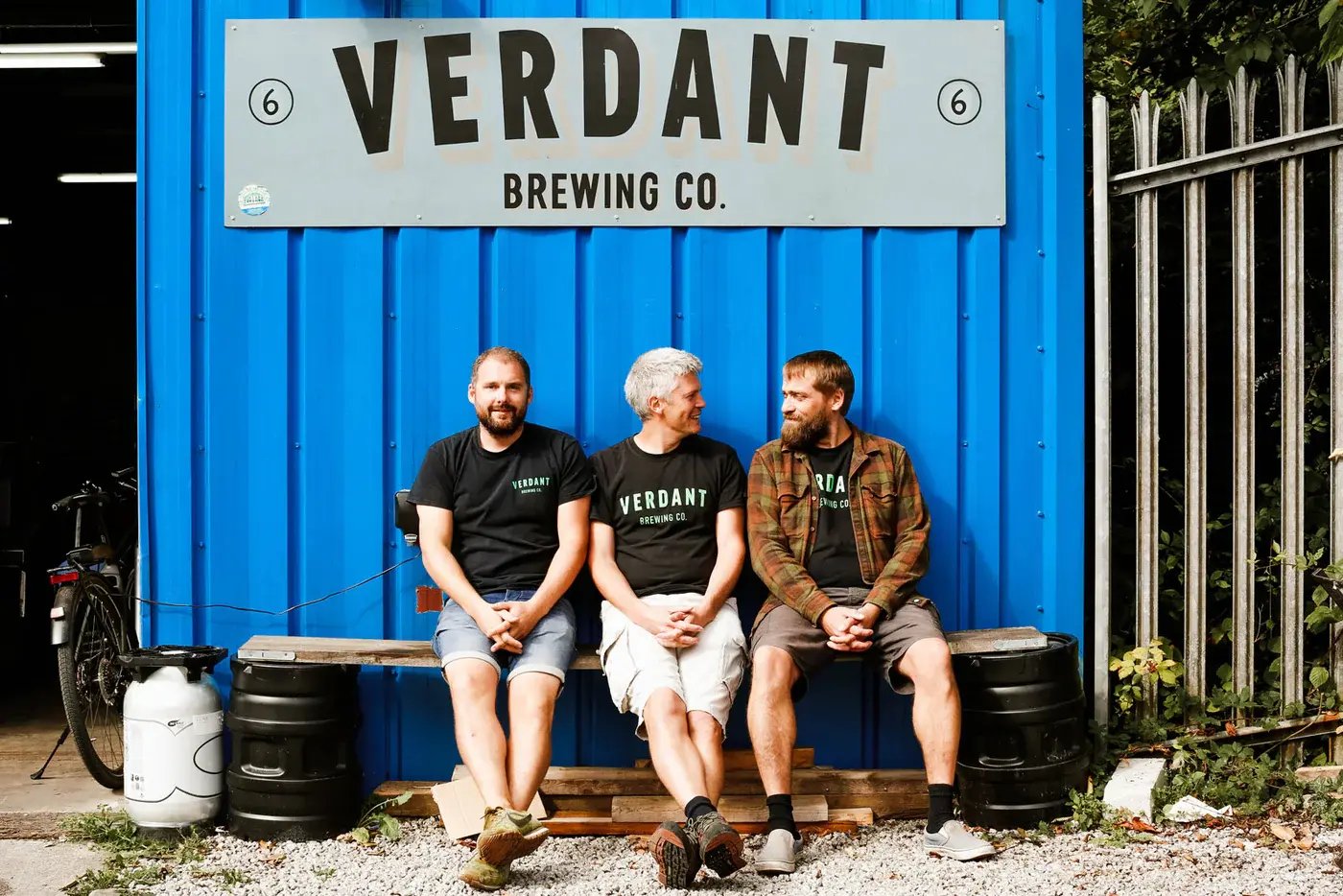
Verdant Brewing Co. Fuels Flexibility and Freshness with Can Supply That Keeps Up
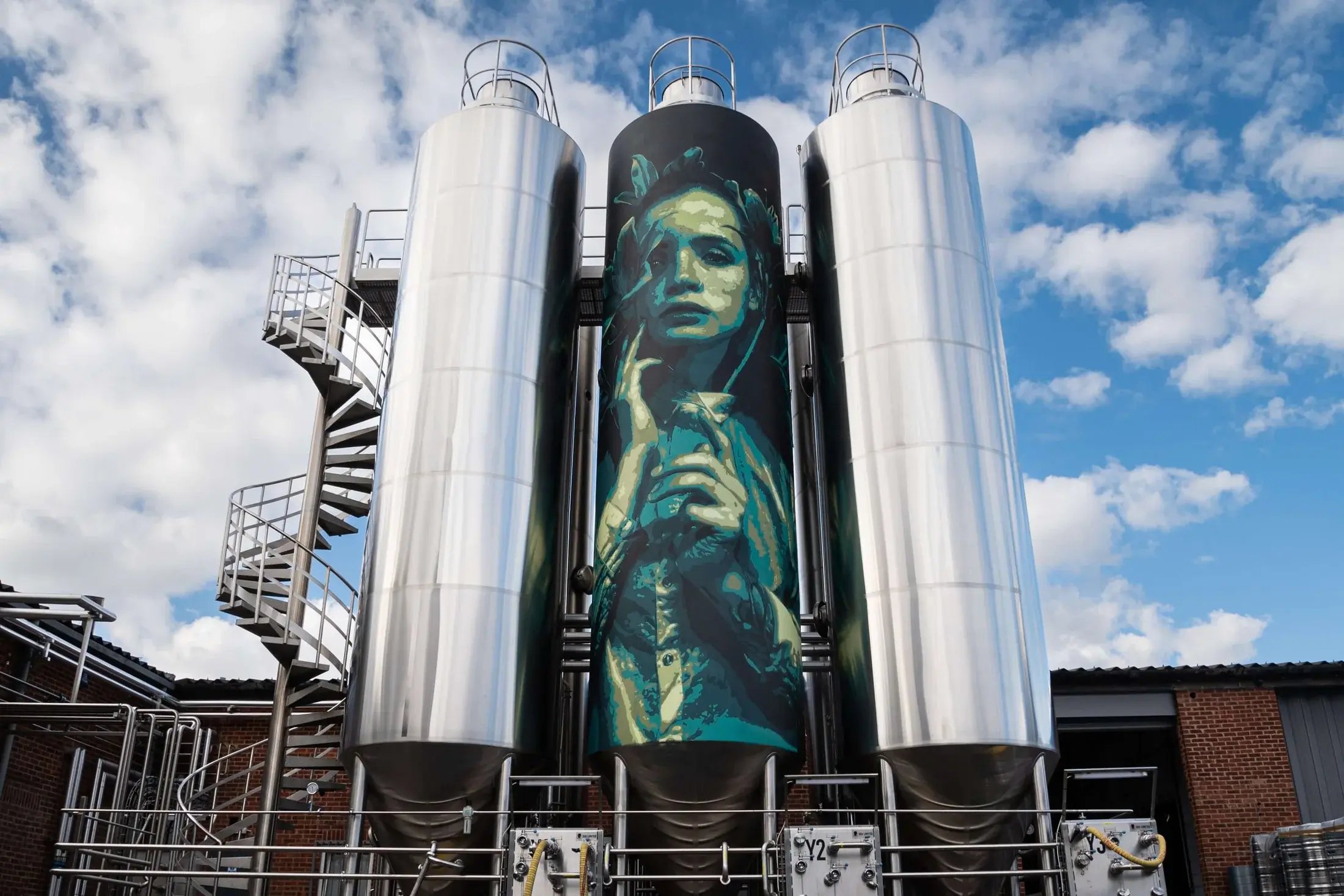
Northern Monk Ditched Direct Supply of 9M Cans Annually In A Bold Move To A Relationship-Driven Distributor
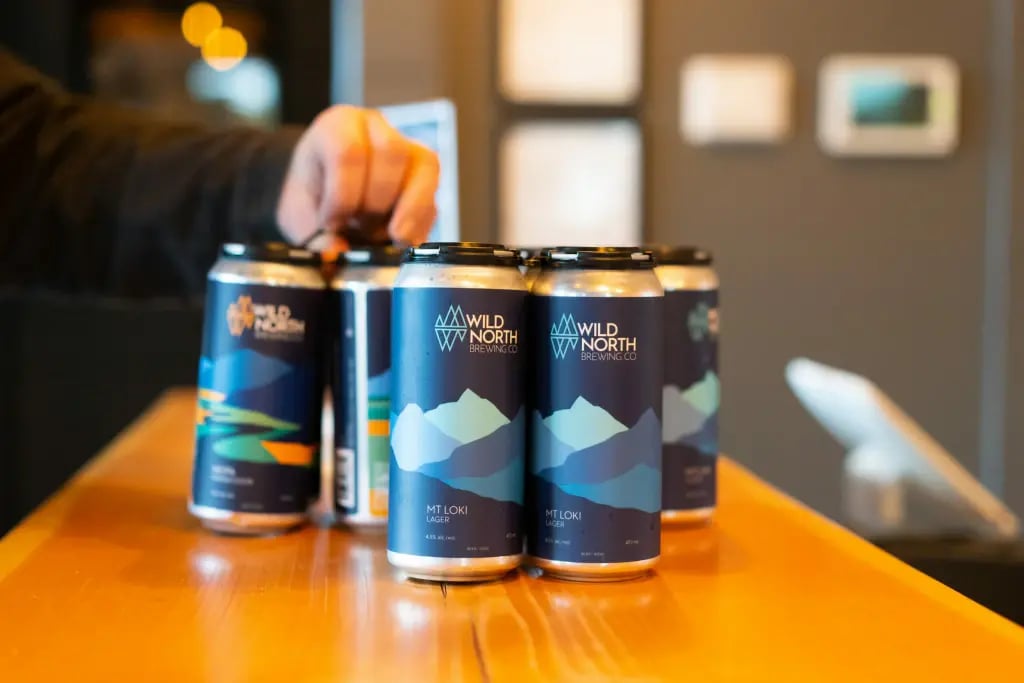